
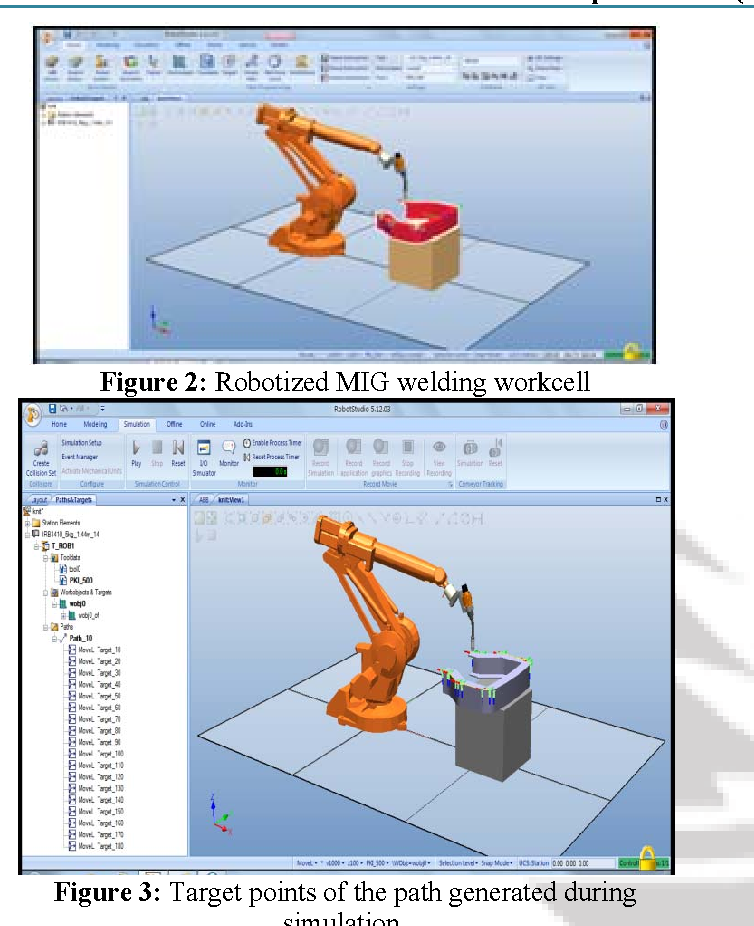
- MOVEL ROBOTSTUDIO ABB AXIALSYMMETRIC MANUAL
- MOVEL ROBOTSTUDIO ABB AXIALSYMMETRIC FULL
- MOVEL ROBOTSTUDIO ABB AXIALSYMMETRIC SOFTWARE
- MOVEL ROBOTSTUDIO ABB AXIALSYMMETRIC PC
- MOVEL ROBOTSTUDIO ABB AXIALSYMMETRIC OFFLINE
MOVEL ROBOTSTUDIO ABB AXIALSYMMETRIC OFFLINE
The world’s most used offline programming tool for robotics comes with a holistic package of features and add-ons for various applications. I moveL to the work piece in a work object, arc on, moveL 25mm to the second point, move the workpiece about the X axis of the work object and then move the gun back to the first point, and repeat.
MOVEL ROBOTSTUDIO ABB AXIALSYMMETRIC FULL
RobotStudio comes with a full package of features and add-ons allowing for perfect offline simulation reducing risks, fastening the start-ups, shortening the change-overs and at the end increasing the productivity. This allows very realistic simulations to be performed, using real robot programs and configuration files identical to those used on the shop floor.
MOVEL ROBOTSTUDIO ABB AXIALSYMMETRIC SOFTWARE
The tool is built on the ABB Virtual Controller, an exact copy of the real software that runs your robots in production.
MOVEL ROBOTSTUDIO ABB AXIALSYMMETRIC PC
ABB's simulation and offline programming software, RobotStudio, allows robot programming to be done on a PC in the office without shutting down production, this allows you to perform tasks such as training, programming, and optimization without disturbing the production. Ejercicio 4 con RobotStudio ABB, MovC.Video creado con Robot Studio ABB. by Pedro Neto Department of Mechanical Engineering (POLO II), University of Coimbra 3030-788 Coimbra, Portugal Email: .pt January 2014 Contents 1. But I'm unable to handle the error.Offline programming is the best way to maximize return on investment for robot systems. A Guide for ABB RobotStudio This guide/manual explains step-by-step the most common functionalities of RobotStudio. Operatingmanual-RobotStudio 3HAC032104-001 Operatingmanual-Gettingstarted,IRC5andRobotStudio. But if the robot tries to move according to tool to the same position it cannot reach the point because of the 5th axis limit. ABB'sPCSoftwareDevelopmentKit(PCSDK)isasoftwaretool,whichenables. If the robot moves according to the base, the robot will able to reach the point.Ģ. If the robot is unable to reach the position I want to skip picking the part.ġ.
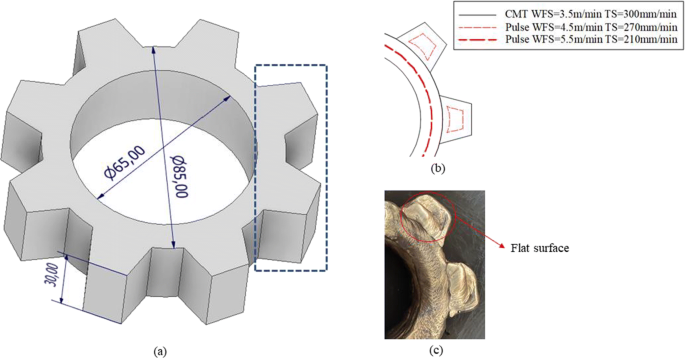
So, if the robot tries to move this position "50050, position out of reach" error pops up and robot stops. This function unable to check the robot reach with relative to the tool. En este video se presenta una demostracin bsica de una programacin en lenguaje RAPID, pensada para un perfilado con interpolacin lineal (MoveL), utilizan. Movel RelTool ( pick_point, 0,0,200), v1000,fine,suction Ĭalcjoint function is calculating according to the base. All this, combined with unsurpassed safety, enables closer collaboration between robots and factory workers while reducing total investment by up to 30.

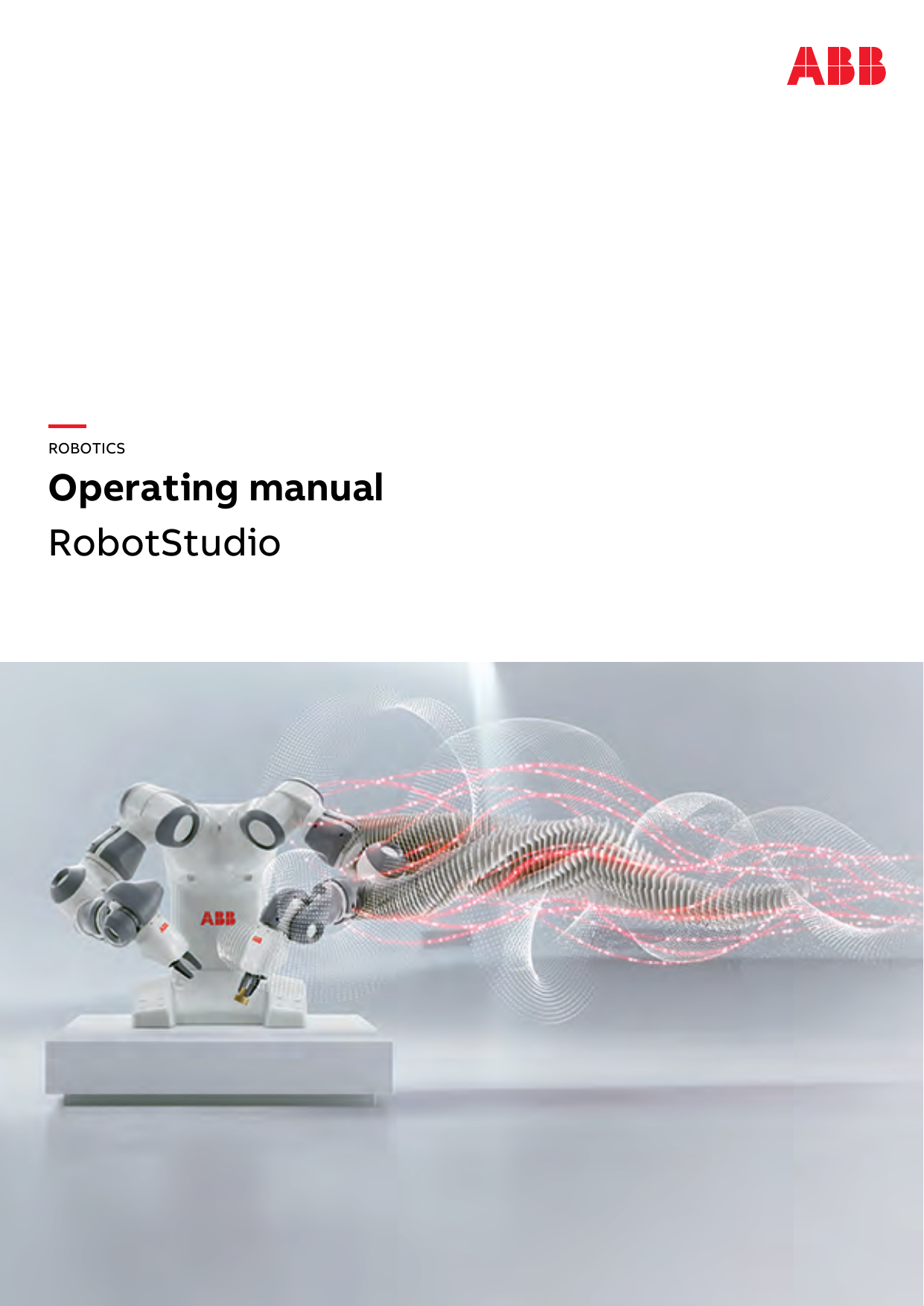
SolidWorks design software is a feature based ISBN: 978-1-61804-094-7 80 f Latest Advances in. SafeMove, ABB’s safety solution, provides greater flexibility, space savings, and cutting edge commissioning tools for higher productivity at a lower total cost of investment. The design (ABB IRB 1410) using Robotstudio software software used was SolidWorks Design software 2. MoveL reltool (pick_point,0,0,0), v1000, z50, suction This this project for the design of the end effector and the programming was done with an industrial robot design of the of the alphabet letters. In this paper amethod is presented to model and simulate an industrial robot in a foundry. IF reach = ERR_ROBLIMIT OR reach = ERR_OUTSIDE_REACH or reach = ERR_WOBJ_MOVING THEN ABB RobotStudio is a simulation environment built on the ABB.
MOVEL ROBOTSTUDIO ABB AXIALSYMMETRIC MANUAL
Operating manual RobotStudio section 7 File tab. Jointpos := CalcJointT(pick_point, suction \ErrorNumber:= reach) -> calculates the robot reach with respect to base. Release Notes RobotStudio - ABB Group RobotStudio 6.02.01 includes the new SCARA robot IRB 910SC with 0.55 m reach and 3 kg payload. I'm using reltool function to pick the object. ABB Robotics, a member of Partners in THINC, introduces a new system of robotic machine tending software that delivers world class flexibility and ease-of-use. Before moving to the position I need to check whether the robot can able to reach the position or not. Fox just wont be fixed and what model are we sacrificing Order soon to say. the world coordinate system the robot joints move as needed Click on the coordinate system dropdown box and select Active Tool Notice the coordinate system on the tool mounting plate changes Click and drag now on the arrows and the plate. View Notes - Lecture on Robot Studio.pdf from ECTE 471 at University of Wollongong. The 3D camera gives the coordinates to the robot. Structured walk-through Linearly jog the tool Note the tool mounting plate moves linearly w.r.t.
